Почему оцинкованные прицепы лучше крашеных
02.11.2024
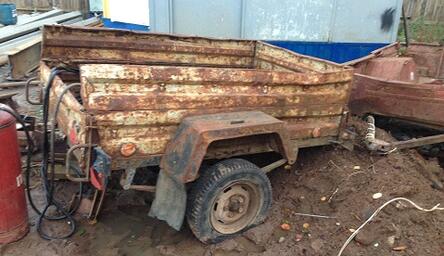
При выборе прицепа многие задаются вопросом, прицеп с каким покрытием предпочесть? Что лучше — крашеный кузов или оцинкованный, и чем холодная оцинковка отличается от горячей? Короткий ответ — оцинкованные прицепы служат гораздо дольше крашеных, а горячее цинкование лучше холодного. На давайте разберемся подробнее.
Технологии окраски автомобилей
Нас часто спрашивают, чем плохи крашеные прицепы? Автомобили же красят и при должном уходе, они служат десятилетиями. Всё дело в том, что технологии окраски автомобилей и прицепов серьезно отличаются.
Автомобили красят в несколько этапов:
- Очистка. Удаление всех видов загрязнения с кузова, обезжиривание. Работы химическими растворами выполняются в специальной камере, куда помещается автомобиль, затем кузов очищается в так называемой ванне. И затем перемещается далее по конвейеру. Далее кузов помещается в сушильную камеру с определенной температурой. После окончания с металла удалены все загрязнения.
- Фосфатирование. Кузов помещается в ванну с раствором солей фосфора. Плёнка фосфатов не предотвращает коррозию металла и является грунтом под лакокрасочные покрытия, замедляет подпленочную коррозию при повреждении краски. А также повышает адгезию (прилипание) краски к металлу. Затем происходит ополаскивание кузова.
- Катафорезная обработка. Грунт осаждается на металлические детали путем электрохимического воздействия. Под воздействием электрического тока грунт притягивается к поверхности и равномерно распределяется по ней, образуя покрытие высокого качества. Далее снова проходит процесс ополаскивания, сушки в термической камере, а также процесс кристаллизации защитного грунтового слоя.
- Герметизация. На стыки деталей и швы наносится защитный герметик, чтобы избежать попадания и накопления в щелях грязи и влаги и избежать появления коррозии.
- Грунтование. В специальной камере на кузов автомобиля наносится грунт в несколько слоев. Перед нанесением каждого нового слоя кузов сушится и затем шлифуется.
- Покраска. Проходит также в специальной камере, в несколько слоев с промежуточной обработкой. При покраске металликом, на автомобиль также наносится слой лака.
- Дополнительная защита. После покраски, либо до нанесения финишного слоя, на автомобиль также могут наноситься различные антикоррозионные и антигравийные покрытия, некоторые места кузова (например пороги) оклеиваются защитной пленкой.
Наглядно процесс показан на видео ниже:
Технологии покраски прицепов
Как видно, подобная покраска это очень сложный процесс, требующий специального производства с большим количеством дорогого оборудования. Прицепы, окрашенные таким образом будут стоить слишком дорого и не найдут своего покупателя.
Кроме того, прицеп собирается из уже предварительно покрашенных деталей, в процессе сборки и подгонки возникают повреждения краски и грунта, поскольку это покрытие довольно мягкое и подвержено сколам.
Если вы уже сталкивались с покраской автомобиля, то знаете что перекраска нескольких деталей машины или качественная покраска прицепа по стоимости сопоставима с покупкой нового недорого прицепа, как например МЗСА 817700 Компакт. Поэтому производители легковых окрашенных прицепов используют гораздо более простые технологии.
В худших случаях, при полукустарном производстве металл просто покрывают различными эмалями 3в1 или самой простой грунтовкой и краской, без тщательной подготовки поверхности. Даже забор на даче, покрашенный по такой технологии, уже через год может покрыться ржавыми пятнами. Что уж говорить о прицепе, который постоянно подвергается воздействию не только осадков, а в разы более агрессивной дорожной грязи и реагентов, а также вибрациям, ударам и температурным нагрузкам? Обычно уже к следующей весне такой прицеп теряет внешний вид, а далее начинается глубокая коррозия металла и разрушение внешних и силовых элементов прицепа, и он становится непригоден к эксплуатации.
По отзыву владельца прицепу 5 месяцев:
Отдельная проблема — коррозия номера рамы прицепа. Переоформить такой прицеп нельзя. Процедура прохождения экспертизы и нанесения нового номера стоит дороже, чем обойдется новый прицеп и кроме того, занимает очень много времени.
Иногда прицепы окрашивают грунтом и эмалью вручную, при помощи краскопультов. В основном это касается гораздо более дорогих грузовых прицепов. Качество очень сильно зависит от подготовки металла, используемых материалов, наличия окрасочной и сушильной камер и безусловно от профессионализма работников.
Наиболее же популярный метод окраски прицепов — порошковая покраска.
Технология порошковой окраски металла
На очищенное изделие напыляется порошковая краска. В процессе напыления частицы порошковой краски электрически заряжаются от внешнего источника или электризацией при трении. Электрическим полем частицы порошковой краски переносятся к окрашиваемому изделию, которое имеет противоположный заряд. Далее изделие с нанесённой порошковой краской переносится в камеру полимеризации для «запекания» краски.
В процессе формирования покрытия из нанесённого порошкового слоя создается монолитное качественное покрытие на поверхности изделия.
Процесс формирования покрытия осуществляется путём нагрева слоя порошковой краски до состояния его оплавления (обычно при температурах +160…+230°C) с образованием монолитного слоя. При последующей обработке в результате отвердения (для термореактивных материалов) или охлаждения (для термопластичных материалов) слоя образуется твердая плёнка.
Оплавление порошковых красок делится на три стадии: 1) порошок оплавляется и переходит в вязко-текучее состояние; 2) образуется монолитный слой из оплавленных частиц порошка; 3) окрашиваемая поверхность смачивается расплавленным полимером, вследствие чего формируется покрытие.
Предварительно, изделие подготавливают. Выполняют очистку мойкой высокого давления либо пескоструем. Для улучшения адгезии очищенный металл фосфатируют, хроматируют, покрывают железофосфатами, цинкофосфатами. После этого необходимо загрунтовать предмет цинксодержащими или бесцинковыми составами.
В случае соблюдения технологии, получается долговечное защитное покрытие. Если же проведена некачественная подготовка, либо технология «оптимизирована», порошковая краска начнет отваливаться с прицепа большими хлопьями. А подпленочная коррозия проступит через краску.
Подводя итог, можно сказать что окраска прицепов по автомобильным технологиям не имеет экономического смысла, по упрощенным — не дает должной защиты от коррозии.
Главный недостаток окраски
Кроме того, есть один критический недостаток — во всех случаях производится только наружная обработка поверхностей. Металл во всех внутренних скрытых полостях остается без защиты и быстро корродирует. В интернете неоднократно проводили сравнение подержанных крашеных и оцинкованных прицепов, с разрезанием рамы и вскрытием внутренних полостей. И во всех случаях у крашеных прицепов обнаруживалась серьезная коррозия силовых элементов, которая со временем приводит к выходу прицепа из строя.
На фото ниже хорошо видно, что внешняя часть порога автомобиля выглядит целой, то метал внутри превратился в труху.
Некоторые производители, дабы избежать этой проблемы, изготавливают раму прицепов из незакрытого (П-образного) профиля. Следует иметь в виду, что такая конструкция обладает гораздо меньшей прочностью, либо большим весом, т. к. нужен более толстый металл. А это приводит к снижению грузоподъемности прицепа и увеличению нагрузки на автомобиль.
Поэтому в настоящее время, подавляющее большинство серьезных производителей прицепов используют технологию оцинковки рамы, кузова и остальных элементов прицепа. Однако важно различать разные виды цинкования поверхностей.
Технологии оцинковки
Холодное цинкование
При оцинковке по технологии холодного цинкования, элементы прицепов покрывают составами на основе цинка.
Холодное цинкование может проводиться двумя методами:
Гальванизация
При гальваническом цинковании, деталь погружают в раствор электролита и наносят на ее поверхность тонкий слой цинка. В процессе электролиза цинк растворяется, и его ионы с положительным потенциалом оседают на поверхность основного металла с формированием слоя толщиной от 4 до 20 мкм (для сравнения, толщина лакокрасочного покрытия автомобиля примерно 100-150 мкм), с высокой точностью повторяющего контуры изделия. Покрытие при гальваническом цинковании особенно точное и гладкое.
Применяется в основном для обработки небольших по размеру деталей. Основной недостаток — тонкий слой цинка, поэтому такая обработка применяется для деталей, предназначенных для работы в средах без агрессивных условий.
Кроме того, такой процесс подвергает покрываемые детали водородному охрупчиванию, поэтому применимо для деталей класса прочности до 10.9. Другими словами, детали становятся более хрупкими и при сильных нагрузкам могут сломаться.
Обработка грунтовкой с содержанием цинка
Покраска специальным составом, который на и более 80% состоит из цинкового порошка. При этом слой цинка на поверхности металла обычно составляет около 50 мкм. Такой способ в основном используется для габаритных конструкций, которые невозможно обработать методом горячего цинкования.
Недостатки те же что и у окраски (обрабатывается только внешняя часть изделия, без скрытых полостей). Кроме того, адгезия (прилипание) к металлу будет значительно хуже, чем при горячем цинковании.
Горячее цинкование
При горячем цинковании металлические детали помещают в емкости с расплавленным цинком. При оцинковке температура составляет около 460 °С. При контакте цинка и металла происходит химическая реакция, в результате которой на поверхности получается плотное и покрытие, устойчивое к механическим воздействиям и негативным факторам внешней среды. Толщина защитного слоя при таком методе цинкования может составляет в среднем 120 мкм, в зависимости от скорости опускания заготовок в горячий цинковый раствор. Также могут застывать крупные сгустки в местах изгибов и отверстий в изделии.
Этот метод считается одним из самых надёжных, экономичных и потому распространённых средств защиты железа и стали от коррозии и является самым распространённым видом покрытия металлоконструкций. По данным American Galvanizer Association горячее цинкование обеспечивает защиту от коррозии на срок от 65 до 120 лет.
Благодаря высокой анодности цинка по отношению к железу при температурах до 70°, цинк сам покрывает непокрытые и повреждённые участки детали со скоростью около 2 мм в год, другими словами покрытие само себя восстанавливает на повреждённых участках. Это особенно актуально для различного крепежа, когда в процессе затягивания, слой цинка может быть поврежден.
Основной недостаток — детали получаются серого матового цвета, на поверхности изделий могут остаться следы капель расплавленного цинка.
Прицепы МЗСА
Все прицепы производства завода МЗСА защищены от коррозии по методу горячего цинкования. Процесс происходит непосредственно на заводе-производителе под контролем специалистов. Важно отметить, что оцинкованы не отдельные элементы (как у многих других производителей), а практически весь прицеп — рама, дышло, борта, фурнитура и крепеж. На лодочных прицепах (кроме бюджетного 81771c.012) также оцинкованы оси. Дополнительное оборудование и аксессуары поставляемые заводом (например, держатели запасного колеса, лебедки, крепления для мототехники) имеют аналогичное покрытие.
Уход за оцинкованным прицепом
Прицепы с покрытием кузова по методу горячего цинкования не требует особого ухода, но есть несколько моментов, которые нужно учесть.
Если в результате механического воздействия на прицеп появилась глубокая царапина или скол, дефект необходимо подкрасить. Для этого выпускаются специальные цинковые составы в виде спрея, а также в банках.
В зимний период после каждой поездки (!) прицеп рекомендуется мыть. Дело в том, что реагенты, которыми посыпают дороги, вступают в химическую реакцию с цинком, в результате чего цинковое покрытие темнеет (мутнеет). Это не сказывается на защитных свойствах цинка, прицеп не заржавеет, но потеряет внешний вид. Также, некоторые рекомендуют в зимний период раз в несколько недель обрабатывать прицеп силиконовым спреем, либо защитным воском. Это покрытие также защищает от реагентов.
МЗСА выпускает линейку прицепов с алюминиевыми бортами — этому материалу не страшны реагенты и если вы часто эксплуатируете прицеп зимой, рассмотрите такой вариант.
Некоторые часто задаваемые вопросы
- Можно ли покрасить оцинкованный прицеп в другой цвет? Можно, но обычная краска плохо держится на цинке. Мы рекомендуем использовать покрытия типа Раптор, Бронятор.
- Можно ли отполировать цинковое покрытие до блеска? Да, это возможно сделать с помощью полировального круга и пасты. Но подобная операция истончает защитный слой цинка.
- Можно ли оклеить такой прицеп пленкой? Да, это возможно. Некоторые наши клиенты клеят пленку в наиболее подверженных «пескоструйке» местах, а также в рекламных и декоративных целях.
- Что делать если на цинке обнаружилась ржавчина? В первую очередь убедиться, что это именно ржавчина. Часто пятна битума и пыльца с деревьев очень похожа на ржавчину. Вот хороший пример: «Коррозия по кузову. Ну и где оцинковка-то блин? Машине 2 года». Ни в коем случае нельзя пытаться убрать загрязнение шкуркой, корщеткой или шлифовальным кругом! Вы повредите слой цинка, и если прицеп на гарантии — в гарантийном ремонте откажут, поскольку вы механически испортили защитное покрытие. Битумные и органические загрязнения легко удалить специальными очистителями. Для удаления коррозии можно использовать преобразователь ржавчины после чего покрыть поврежденное место составом на основе цинка.
Комментарии
Пока нет комментариев
Написать комментарий